1、施工工艺
本工程新增立柱灌注桩采用正循环钻进,自然造浆泥浆护壁成孔,正循环清孔方法,商品砼导管回顶法水下砼灌注的成桩工艺。
1)、本工程我公司将投入、扭矩大、性能稳定的GPS-10型工程钻机施工钻孔灌注桩。
2)、钻进以自然造浆的泥浆工艺,每套钻机配备一个泥浆循环池,泥浆池体积大于成孔实际体积的1.5倍,便于各机台在钻进中根据地层特点及时调整泥浆性能。
3)、为保证施工速度及成桩质量,本工程下放导管,下放钢筋笼以及钻机就位及移动,将全部采用灌注桩机及吊车设备进行辅助作业。
.2、施工工艺流程图
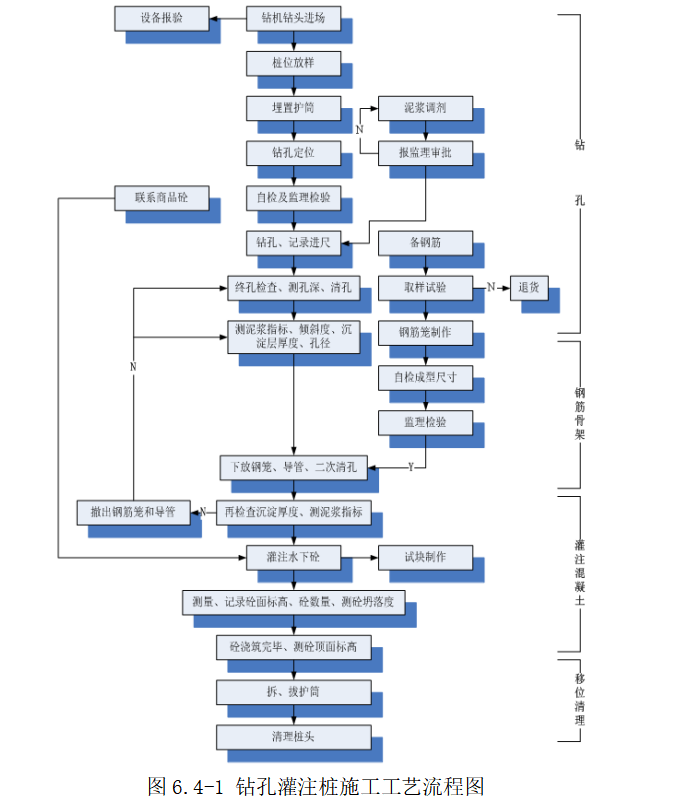

3试成孔
根据设计要求,本工程钻孔灌注桩施工前,需进行试数目不少于2个的成孔。
1)试成孔目的
了解土层施工特点,检验所选设备、机具、施工工艺及技术要求是否适宜设计要求,并为分层成孔钻进和选择最佳成孔及成桩技术参数提供实际依据。
2)试成孔位置
钻孔灌注桩的试成孔共2根,在第一阶段施工,第一个孔主要了解土层情况及施工特性;第二个孔进行孔壁稳定性测试,依据这两组测量结果判断孔壁稳定情况。成孔完成后除测量孔径、垂直度、孔深、沉渣厚度外,还需测定成孔后停滞一段时间后孔径不小于设计直径及沉渣厚度,以评定孔壁的稳定性及施工工艺的可靠性。
根据相关设计要求,试成孔完成后应模拟实际工况进行清孔。然后进行试成孔连续跟踪监测,试成孔跟踪测试时间为36h,每隔4h每隔4小时进行一次成孔质量监测。
具体项目清单如下:
(1)成孔深度控制:成孔至设计深度后,应对孔深进行检测,以便清孔后计算沉渣厚度;
(2)孔径采用孔径仪或超声波测量,桩径允许误差:0~+50mm;
(3)垂直度允许误差:不大于1/300
(4)孔壁泥浆护壁效果观察;
(5)孔底沉渣厚度检测:不大于100mm。
(6)其他业主或监理认为需要检测的内容。
根据试成孔的成孔质量检测清孔分析改进成孔工艺,在对每一层土质的钻进参数优化、改进,对钻机垂直度、泥浆指标的控制做到勤测、勤纠,力争通过试成孔施工将机械设备性能、地质情况以及人员是否熟练操作的情况摸透,在试桩施工时有针对性的改进和优化。
.4、施工方法
各道工序的具体施工方法及要求如下:
(1)、测量定位:
测量定位:使用全站仪测量放线,开挖沟槽,按设计桩位进行布桩;桩位方向距离误差小于10mm;利用S3型水准仪来测定护筒及桩机平台标高,其误差不大于1cm。
(2)、埋设护筒
护筒采用4mm钢板卷制而成,护筒内径大于桩直径100mm,为防止钻进施工中护筒外圈通浆造成塌孔和护筒脱落,护筒应埋入好土20cm,四周用粘土填密实,其中心与桩位中心允许误差不大于20mm,并应保持护筒垂直度和水平度,为确保桩位的准确。
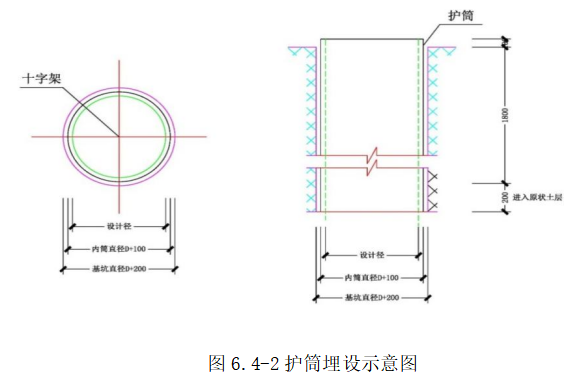
(3)、钻机就位
钻机就位后,用水平尺调整桩机的水平度,钻机就位后转盘水平度指标误差不大于1″。
(4)、成孔工艺
钻孔灌注桩全部采用正循环,刮刀回转钻进成孔,自然造浆护壁,正循环两次清孔工艺、导管回顶法灌注成桩。
1)、钻进技术参数
根据桩孔施工地层特点及相邻地段施工经验,钻进技术参数为:压力500~1500kg(自重加压),转速30~100rpm,泵量30~108m3/h。
在易缩径的粘土层中,应适当增加扫孔次数以防止缩径,对硬塑层采用大压力快转速钻进,以提高钻进效率,砂层则采用中等压力,慢转速并适当增大泥浆比重和粘度。
上述方法优点是回转阻力小,桩孔垂直度好,孔底沉渣少,钻进速度合理,在确保质量的基础上有较高的效率。
2)、桩孔质量检测
桩孔质量参数包括:孔深、孔径、钻孔垂直度、沉渣厚度。
孔深:钻孔前先确定护筒标高,以此为起点按设计要求的孔底标高确定孔深,以钻杆长度测量孔深。
孔底沉渣以第二次清孔后测定为准,清孔后双排段灌注桩、立柱桩沉渣厚度不超过50mm,支护桩沉渣厚度小于100mm。
1)、护壁与清孔泥浆性能要求:
A、注入孔口泥浆性能技术
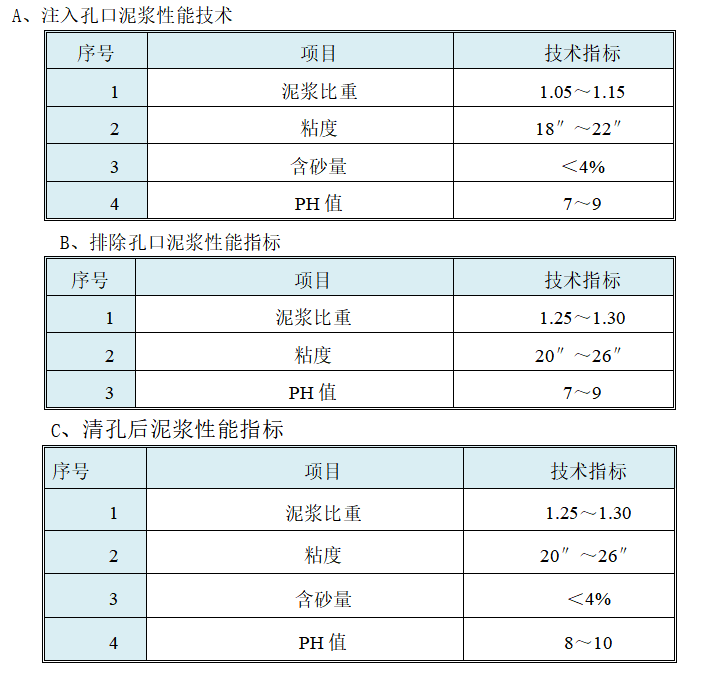
依据本工程岩土工程地质资料,该区域泥浆护壁采用地层自然造浆为主,并根据不同地层的地质特性,调整泥浆性能,以确保泥浆能充分携砂以减少孔底沉渣和保持孔壁的稳定,具体分层位泥浆性能如下表:
4)、清孔方法:
第一次清孔:桩孔成孔后,应进行第一次清孔,清孔时应将钻具提离孔底0.3—0.5米,缓慢回转,再加大泵量,每隔10分钟一次,将钻具提高3—5米来回串动几次,再开泵清孔,确保第一次清孔后孔内无泥块,比重为1.25左右。
第二次清孔:钢筋笼、导管下好后,用导管进行第二次清孔,二次清孔时间不小于30分钟。确定孔底沉渣厚度≤5cm时,方可停止清孔。
测定孔底沉渣,应用测锤测试,测绳读数一定要准确,用3~5孔后校正一次。
清孔结束后,应尽快灌注砼,其间隔时间不能大于30分钟,超过时要重新测淤,二次清孔后的泥浆比重应控制在小于或等于1.20,以确保孔壁稳定。
综合泥浆性能指标为:
钻进成孔泥浆比重1.20~1.35,二清应小于或等于1.20,粘度20″左右。
1)、以上所有成孔技术参数均应根据试成孔施工情况、检测结果加以确定。
5)、终孔后成孔检测:
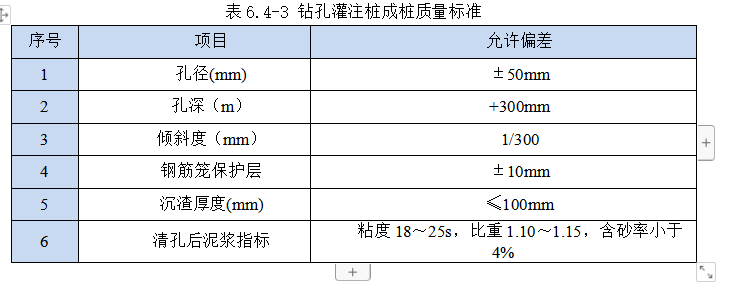
.5钢筋笼加工制作及安装
1)钢筋笼制作
(1)钢筋笼分节制作,分节长为9mm,采用直螺纹连接分节吊放,吊拼机械连接接而成;主筋机械连接以50%错开。
(2)钢筋笼制作前,应将主筋校直、除锈,下料长度要准确;
(3)钢筋笼制作允许偏差:

(4)主筋保护层为50mm,允许偏差为±10mm,为保证保护层厚度,每节钢筋笼设置两组混凝土保护快,每组三块,均匀错开。
(5)环形箍筋、螺旋箍筋与主筋的连接采用直接点焊固定。
(6)成型钢筋笼应平卧堆放,且不得超过二层。
(7)现场使用钢筋必须具有质保书,并经
现场抽样检测后方可使用,钢筋以同一炉批号每

60T抽检一组。
(8)为保钢筋笼成型均匀美观,本项目采用自动滚笼机缠绕螺旋筋工艺,确保螺旋筋间距均匀且牢固。
2)钢筋笼安装
a.钢筋笼安装时为保证不变形,采用两点起吊,以免单根钢筋受力,使其变形。起吊钢筋笼的起吊端,而后缓缓起吊,直至钢筋骨架同地面垂直。检查钢筋骨架是否顺直,如有弯曲应调直。
b.钢筋笼第一节放入孔内后,在顶上第一道加强圈下穿两根横担,然后搁置在机台上,同样方法再起吊第二节,上下笼对正位置后孔口接丝。接丝完毕起吊钢筋笼,取出横担,钢筋笼缓慢下沉放入孔内,待到笼子顶部第一道加强圈时焊接吊环钢筋(见图6.4-22),将钢笼放至设计标高。
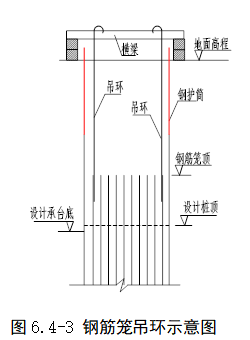
c.钢筋笼在下放时应注意防止碰撞孔壁,如放入困难,应查明原因,不得强行插入。
d.吊放钢筋笼入孔时应对准钻孔,保持垂直,慢放入孔。入孔后不宜左右旋转,徐徐下放并严防孔口坍塌。若遇阻碍应停止下放,查明原因进行处理,严禁猛提猛落和强制下放。
e.在孔口接长钢筋笼时,上、下主筋位置应对正,保证钢筋笼接长后上下段的轴线在一直线上。无论是接长钢筋笼还是钢筋笼全部节段安装到位,在孔口均应有可靠的支撑及固定。
f.钢筋笼吊放入孔后,在顶部钢筋笼上设置两根HRB400直径16的钢筋吊筋,吊环钢筋一端与钢筋笼顶部钢筋单面焊接,另一端焊接固定在桩机上。
G.钢筋笼下孔要吊直,扶稳,缓慢下入以防碰撞孔壁,节与节要清除接头污泥,固定后方可对接,为了保证同心,焊接时要扶正,立焊采用单面焊,焊缝长度大于10d,焊接应饱满(b>0.7,h>0.3D)不损伤主筋,焊渣随焊随敲,吊装过程中在机台两个垂直方向架设线锤控制钢筋笼的垂直度不大于1/200,按图纸要求验收,合格后方可下入孔内。
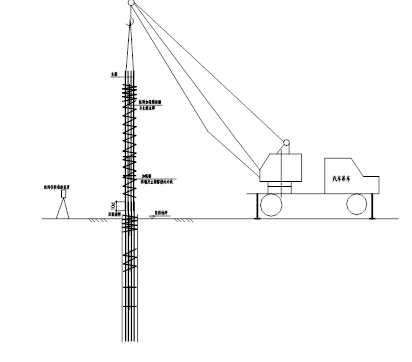
.6、混凝土的灌注
(1)、商品混凝土
所选择的商品混凝土供应站必须是取的相应的资质,对商品混凝土供应站供应的每批商品混凝土,必须向施工单位提供商品混凝土质量证明书。本工程灌注桩设计混凝土强度为C30水下(围护)、C35水下(立柱) ,商品混凝土坍落度控制在20cm±2cm,现场不得任意加水,每根桩做1次坍落度,浇筑前进行坍落度测试。
(2)、混凝土的灌注
因施工场地的限制,本工程可根据现场实际条件采用自卸混凝土或泵送混凝土。灌注采用“导管回顶自密实法”进行灌注,导管下至距离孔底0.3~0.5m处,导管使用Φ250mm规格,灌浆导管使用前须经过过球和压水试验,确保无漏水、渗水时方能使用,灌浆管接头连接处须加密封圈并上紧丝扣。
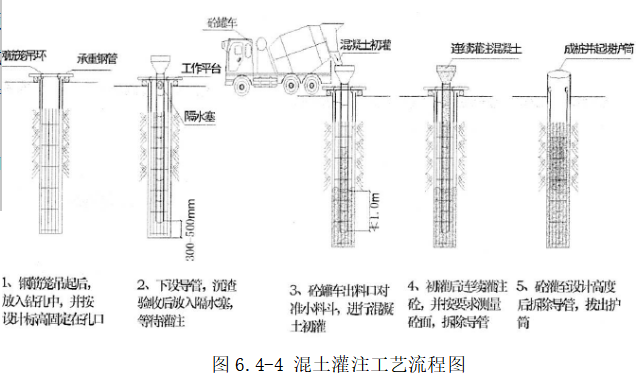
(3)砼初灌量的计算:
水下混凝土灌注砼初灌量是水下桩砼灌注的关键环节,初灌后导管埋深≥0.8m,初灌量根据导管底部距孔底0.5m,不同桩径按公式分别计算,采用不同的初灌斗进行灌注。
初灌砼量计算按下式计算:
2h2k+
d2h1
初灌量计算示意图见下图示。
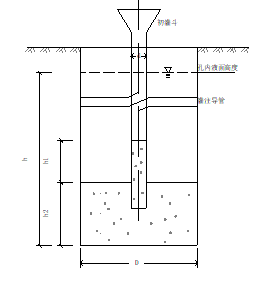
式中: V -混凝土初灌量(m3);
D -桩孔直径(m);
h2-导管埋管深度,一般不小于0.80(m);
d -导管内径,取0.25m或0.30m;
k -混凝土充盈系数,岩溶区取1.3;
h1-孔内砼达到埋管高度时,导管内砼柱与导管外水柱压力平衡所需的高度(m),
即:h1 = (h-h2)
式中: h -桩孔内液面至孔底深度(m);
γw-泥浆比重(KN/m3);
c-砼比重(KN/m3)。
经过计算,直径800的灌注桩(48m)的初灌量为2.2m3,直径800的灌注桩(32m)的初灌量为1.54m3。
(4)混凝土浇筑施工要点
本工程采用Φ250mm导管进行水下砼灌注,水下C35。施工前进行配合比验证,并审核通过。浇筑时采用机架安装导管进行,具体操作如图所示。

砼灌注质量应按下列要求控制:
1)采用商品混凝土,级配单应在混凝土开浇时随车附来。严格把好质量关,每批进场混凝土搅拌站必须附送级配单。现场应仔细核对配合比组成情况,发现问题及时阻止更正。搅拌站后期附送混凝土质量证明单。
2)导管下入孔内之前应仔细检查连接丝扣、焊点及密封槽的好坏,并编号、丈量、记录长度,导管底口距孔底高度控制在30cm左右,且第一节导管长度应大于4m,以保证初灌时埋入砼面大于1.5m。
3)水下混凝土的灌注应在第二次清孔后30min内进行,若超过30min应重新测量孔底泥浆厚度,如不符合要求应进行重新清孔。
4)混凝土隔水塞的大小要与导管的内径相符。
5)混凝土灌注前安放好隔水塞后,导管提离孔底30cm,当导管灌满混凝土,剪断悬挂混凝土隔水塞的铁丝,第一斗混凝土灌入后导管埋入混凝土面1.5m,第一斗混凝土灌注后不得提升导管。
6)水下混凝土灌注应连续进行,导管埋深应控制在3~6m,但最小埋深不得小于2m,导管应勤提勤拆,应经常测定混凝土面高度,以确定提管长度,切不可将导管提出混凝土面以上。
7)注意检查导管吊绳及井口台板的质量,发现问题及时更换,并注意钢筋笼的固定情况,防止跑笼。
8)混凝土灌注高度应高出不宜小于桩长的3%,且不宜小于2m,由施工员测定后方可停止灌注。
9)单桩灌注时间宜不大于8小时,与二次清孔验收时间间隔应≤0.5小时。
10)灌注完毕后,待混凝土初凝后即可切断钢筋笼吊筋,拔出护筒,清洗导管和护筒,清除孔口泥浆(灌注时排出的废泥浆引入排污池),然后回填孔口,以保证施工现场安全文明。
11)按规定由专人做好混凝土试块的制作,每根桩做混凝土试块一组,注明日期、桩号,按标准养护28天,送检测单位检测强度。
12)、每桩灌注应连续进行,且总时间不得超过8小时。
13)、成孔完毕至灌注混凝土时间间隔不得超过24小时。
14)、混凝土浇筑完毕且达到72小时方可施工相邻的桩。